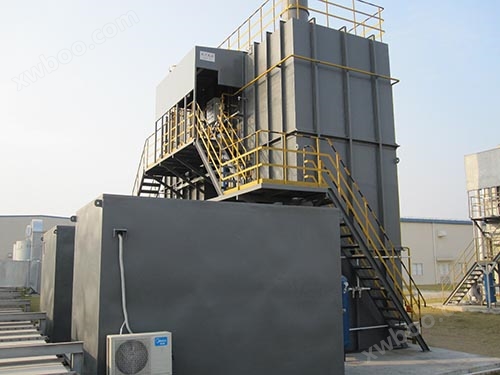
Heat the organic waste gas to above 760 degrees Celsius to oxidize and decompose the VOCs in the waste gas into carbon dioxide and water. The high-temperature gas generated by oxidation flows through a specially designed ceramic heat storage body, causing the ceramic body to heat up and "store heat", which is used to preheat the organic waste gas that enters later. Thus saving fuel consumption for exhaust gas heating. Ceramic thermal storage bodies should be divided into two or more zones or chambers, with each chamber undergoing a sequence of thermal storage, heat release, and cleaning, repeating the process and working continuously.
System features:
1. Adopting a thermal storage heat exchange device, the thermal storage carrier directly exchanges heat with the gas, resulting in high furnace radiation temperature and pressure, and fast heating speed; The low-temperature heat transfer effect is significant, so the heat transfer efficiency is particularly high.
2. The temperature inside the heat storage chamber is uniformly graded and increased, which enhances heat transfer inside the furnace and improves the heat exchange effect. Therefore, the furnace volume of an oxidation furnace with the same processing capacity can be reduced, greatly reducing the cost of equipment.
3. The high-temperature flame oxidation zone has been expanded, and the boundary of the flame has almost extended to the boundary of the furnace, thereby making the temperature inside the furnace uniform. This not only improves the purification efficiency, but also extends the furnace life.
4. The temperature inside the oxidation chamber increases overall and becomes more evenly distributed; The furnace temperature can reach 760-800 ℃, with low airflow velocity and fast oxidation rate. The flue gas stays at high temperature in the furnace for a long time, and the organic matter is completely oxidized and decomposed.
5. The system adopts PLC automatic oxidation control, with high degree of automation, stable operation, and high reliability;
6. According to the exhaust gas situation, a heat recovery device can be reasonably set up, which can be connected to a heat exchanger, heat transfer oil furnace or waste heat boiler in the high-temperature oxidation chamber; Low temperature flue gas is used to heat exhaust gas and fully utilize the waste heat in the treatment of exhaust gas.